钢铁行业50项极致能效技术(上)
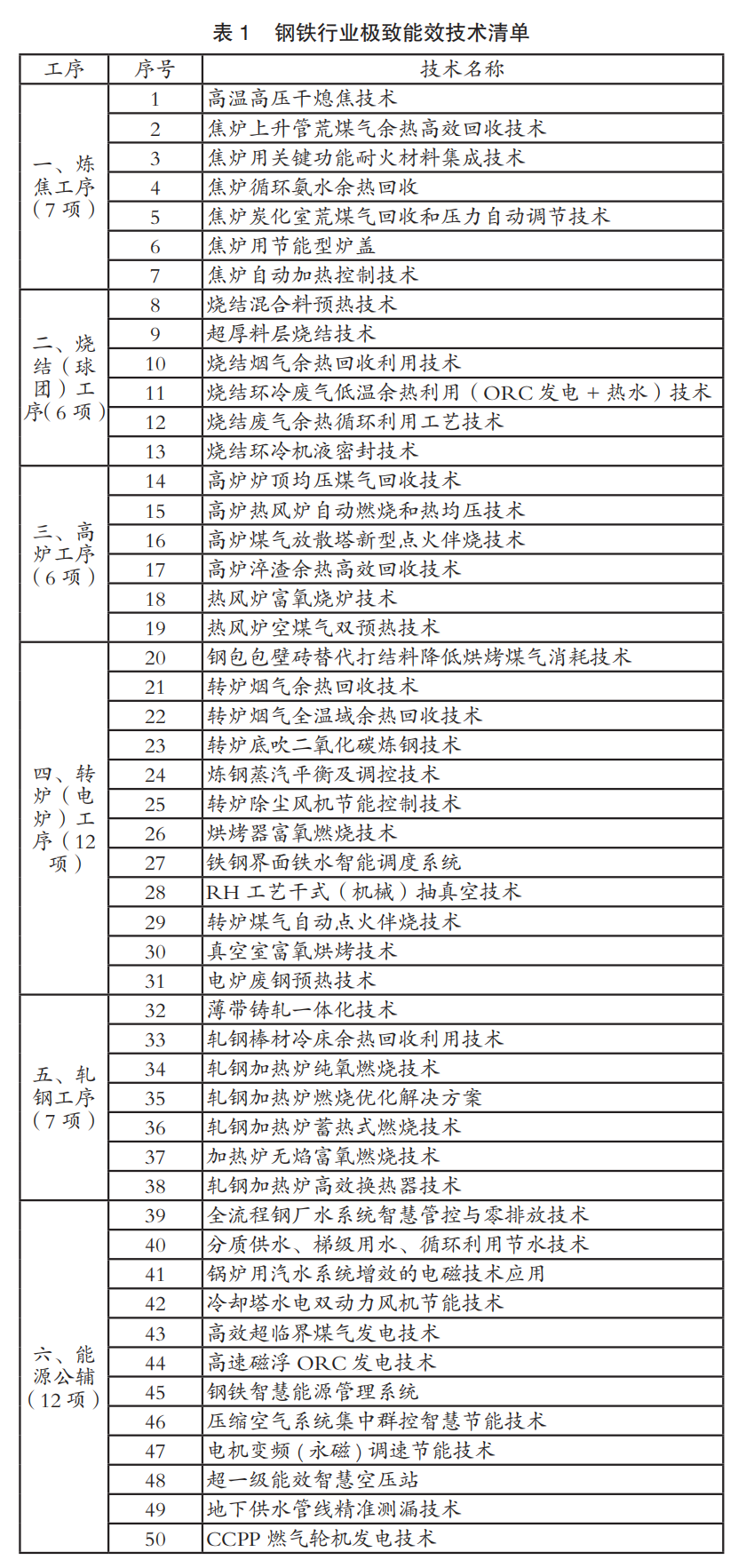

一
炼焦工序
1 高温高压干熄焦技术
技术简介:以N₂为主要成分的循环气体冷却高温焦炭,气体热载体又将热量传给锅炉的换热面产生高压蒸汽,而循环气体得到冷却。在循环风机的作用下,惰性气体在熄焦系统内不断循环,将焦炭的温度从1000℃冷却到250℃以下。与传统中低温干熄焦工艺相比,高温高压干熄焦蒸汽压力提高一倍,温度提高80℃左右,用于发电可大幅提高发电效率;还可改善焦炭质量、减少炼焦生产熄焦过程对环境的污染。
2 焦炉上升管荒煤气余热高效回收技术
技术简介:将原有的焦炉上升管替换为上升管换热器,约800℃的荒煤气流过上升管换热器将热量传递给强制循环的传热媒介,例如循环水、导热油,生产饱和蒸汽、过热蒸汽、高温导热油输送至热用户利用,实现荒煤气余热回收。
3 焦炉用关键功能耐火材料集成技术
技术简介:该集成技术包括表面复合陶瓷成型技术、高导热硅质材料制备技术及窑炉热修补技术等系列技术。焦炉炉门结构大型化,表面光滑,解决了原用小型砖材料的结构不稳定,密封不严气体外溢的环境污染问题。高导热硅砖替代传统的硅砖耐火材料,导热效率显著提高,提高炭化室硅砖的导热性,并保持了其他良好的物理化学性能。
4 焦炉循环氨水余热回收
技术简介:焦炉循环氨水温度达70-80℃,循环量大,含余热量大。通过溴化锂制冷机组以水为制冷剂,溴化锂水溶液为吸收剂,利用水在高真空条件下低沸点汽化特征,回收循环氨水的热量实现制冷。
5 焦炉炭化室荒煤气回收和压力自动调节技术
技术简介:根据每孔炭化室煤气发生量变化,实时调节桥管水封阀盘的开度,实现整个结焦周期内炭化室压力调节,避免在装煤和结焦初期因炭化室压力过大产生煤气及烟尘外泄,并减少炭化室内荒煤气窜漏至燃烧室,实现装煤烟尘治理和焦炉压力稳定。同时技术可调控压力,避免吸入空气造成能耗上升。
6 焦炉用节能型炉盖
技术简介:新型炉盖内设空气隔热层降低了炉盖导热系数,可以减少炉盖部位的热损失,进而可以降低焦炉炉顶面温度,改善炉顶作业区域的环境温度。
7 焦炉自动加热控制技术
技术简介:针对焦炉加热过程调控复杂、加热煤气消耗量大、碳排放高、氮氧化物生成多等难题,开发了炼焦过程智能测温加热控制、焦炉边火道热工控制、炼焦终温反馈调节及焦炉源头减氮控制技术,有效解决焦炉人工控温火道测控精度差、调节滞后的问题,实现焦饼中心温度远程自动准确测量控制,降低焦炉烟气氮氧化物排放。
应用情况:技术在鞍钢等多家钢铁企业推广应用。以1000万吨焦炭产能为例,年可节省标煤6.2万吨,减排16万吨CO2、1357吨NOx、1561吨SO2。
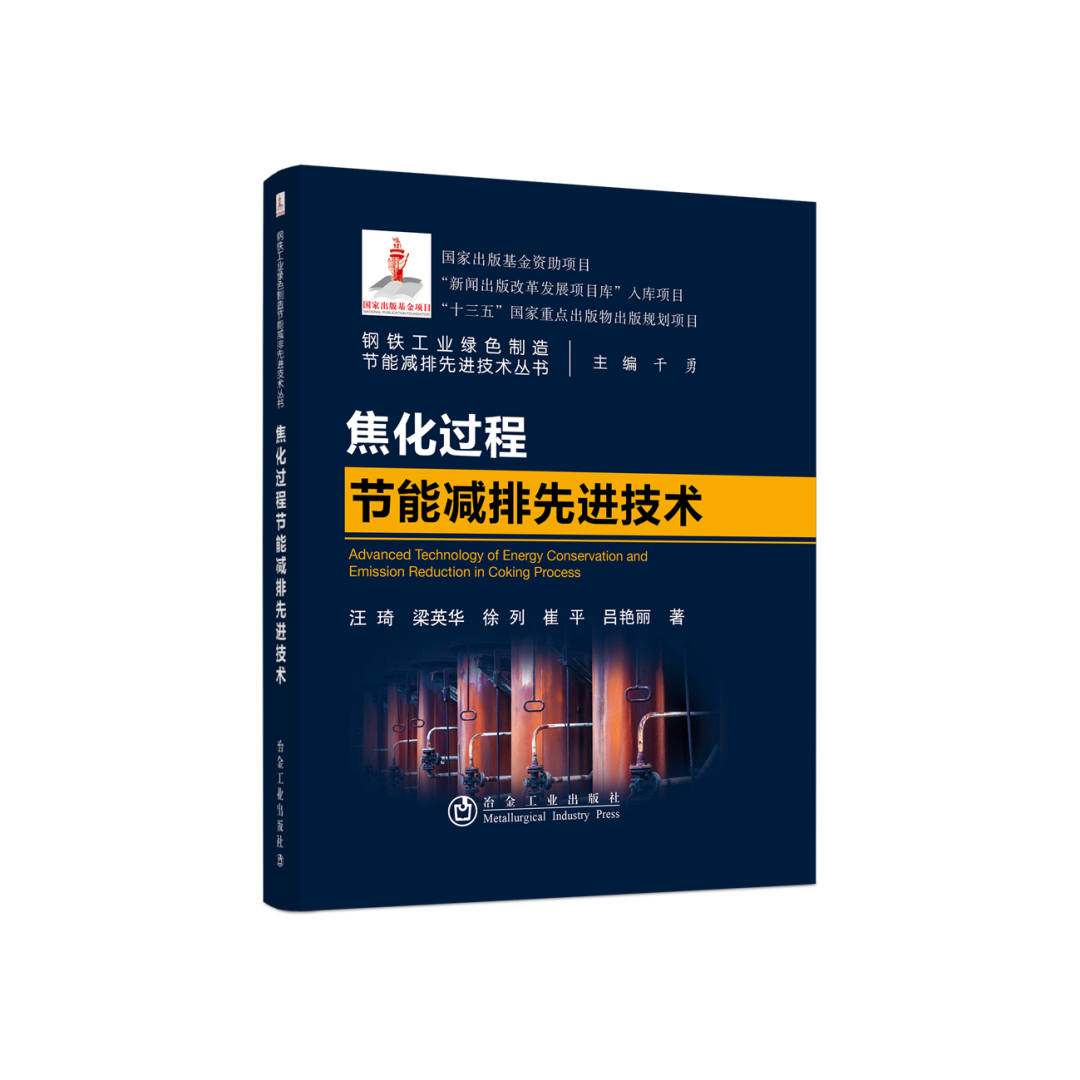
二
烧结(球团)工序
8 烧结混合料预热技术
技术简介:烧结混合机通过使用大量蒸汽的方式预热混合料,其热量利用率偏低,不仅造成蒸汽浪费,而且蒸汽中水分对烧结过程造成影响。通过对制粒工艺优化(将传统一混加水、二混制粒造球和三混强化制粒的方式改为一混强力混匀、二混加水制粒造球和三混强化制粒方式),极大地提高了生石灰粉消化放热功效,全年烧结混合料温度保持在60℃以上,有效降低烧结固体燃料消耗。
9 超厚料层烧结技术
技术简介:超厚料层(1000mm及以上)烧结充分利用料层自动蓄热的原理,通过上层物料的气流对下层物料进行加热,更多地利用料层物料燃烧产生的热量。通过高生产效率、低温烧结、低耗烧结,促进复合铁酸钙生成、改善烧结矿质量等,提升烧结技术经济指标。
10 烧结烟气余热回收利用技术
技术简介:设置烧结大烟道余热锅炉和环冷机双压余热锅炉,回收利用环冷机中高温段废气余热及烧结大烟道尾部风箱高温排烟余热,余热锅炉产生蒸汽用于发电。
11 烧结环冷废气低温余热利用(ORC发电+热水)技术
技术简介:将环冷机三、四段产生的100-220℃左右的热废气送入热交换器内进行热回收,生产热水,或直接用作蒸发ORC工质,驱动ORC机组发电。
12 烧结废气余热循环利用工艺技术
技术简介:烧结低温废气自烧结支管风箱/环冷机排出后,再次被引入烧结料层,因热交换和烧结料层的自动蓄热作用,可将其中的低温显热供给烧结混合料。同时,热废气中的二噁英、PAHs、VOCs等有机污染物在通过烧结料层中高达1200℃以上的烧结带时被分解。因此,利用废气循环烧结不仅可以实现余热的利用,而且大幅度削减了废气排放总量。
13 烧结环冷机液密封技术
技术简介:通过两相动平衡密封技术、高效传热技术、气流均衡处理综合技术、复合静密封技术以及高温烟气循环区液体防汽化技术,减少环冷机漏风率,降低鼓风机电耗,增加环冷蒸汽产量。
应用情况:技术在多家钢铁企业应用。某钢企应用该技术后,实现余热回收产蒸汽80kg/t矿(1.8MPa,270℃)以上。
三
高炉工序
14 高炉炉顶均压煤气回收技术
技术简介:设置炉顶均压煤气回收系统,料罐放散煤气经炉顶旋风除尘器一次除尘、布袋除尘器二次除尘后,再并入净煤气管网,回收废弃能源。采用自然回收工艺,基于料罐内与煤气管网压差连续回收炉顶均压煤气,可适应超低排放要求,设有煤气回收和常规放散两种操作模式,可根据生产需要实现在线切换。
应用情况:技术在多家钢铁企业应用。某钢企生产实践显示,均压煤气回收率可达到85.1%,均压煤气回收量83.8Nm3/次,煤气回收量达3.90Nm3/t铁。
🔍点击封面了解更多
图文来源:《世界金属导报》48期 B14
文章转自:世界金属导报
联系我们
电话:010-6401 5784
邮箱:service@mip1953.com
地址:北京市东城区嵩祝院北巷39号
网址: www.mip1953.com
国务院国有资产监督管理委员会 | 国家新闻出版署 | 国家发展和改革委员会 | 科学技术部 | 工业和信息化部 | 中国钢铁工业协会 | 冶金网
Link
友情链接
Copyright © 冶金工业出版社有限公司 www.mip1953.com 版权所有 | 京ICP备05032908号 京公网安备11010102003462号 | 网络出版服务许可证:网出证(京)字第122号